High Pressure Die Casting Mold: A Key Element in Metal Fabrication
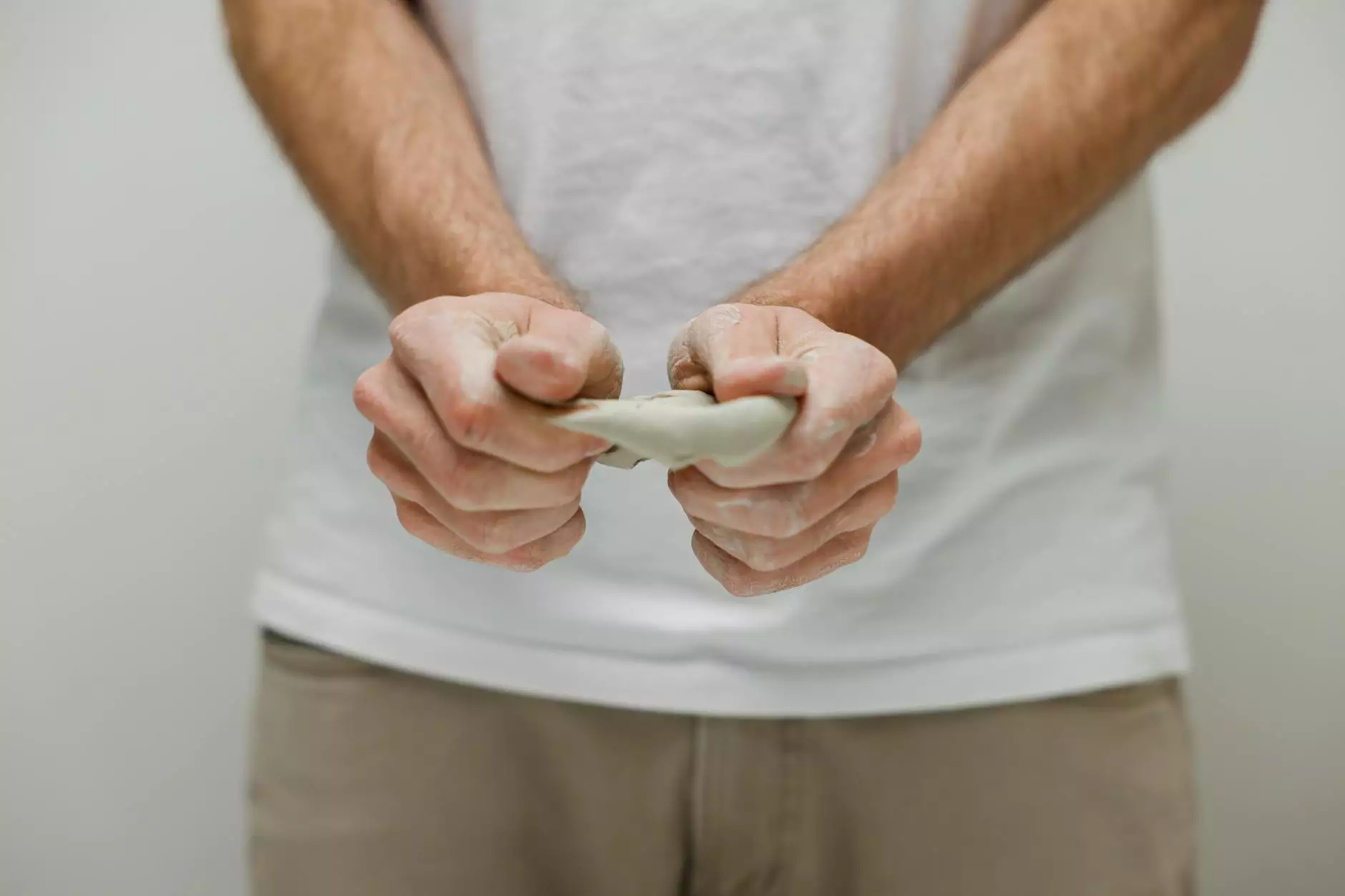
In the realm of metal fabrication, one process that stands out for its efficiency and precision is high pressure die casting mold. This advanced manufacturing technique offers unparalleled benefits for producing intricate and durable metal components. In this article, we will explore the fundamentals of high pressure die casting molds, their operational principles, advantages, applications, and the future of this remarkable technology.
Understanding High Pressure Die Casting Mold
High pressure die casting mold is a process used for producing metal parts by forcing molten metal into a mold cavity under high pressure. This method is primarily used with non-ferrous metals, such as aluminum, zinc, and magnesium. The precision and repeatability of this process make it an invaluable technique in the manufacturing industry.
How Does High Pressure Die Casting Work?
The high pressure die casting process involves several key steps:
- Preparation of the Mold: The die is preheated to a specific temperature, ensuring optimal conditions for casting.
- Injection of Molten Metal: Molten metal is injected into the mold cavity under extreme pressure, often exceeding 1000 PSI.
- Cooling: The molten metal cools and solidifies, taking the shape of the mold.
- Ejection: Once cooled, the die opens, and the newly formed part is ejected.
Advantages of Using High Pressure Die Casting Mold
The use of high pressure die casting mold offers numerous advantages that make it a preferred choice for manufacturers:
- High Precision: The mold creates parts with excellent dimensional accuracy and surface finish.
- Cost-Efficiency: Although the initial cost of the mold may be high, the efficiency of the process reduces overall production costs.
- Rapid Production: High production rates can be achieved, making it suitable for mass manufacturing.
- Versatility: Suitable for a wide range of applications in various industries, including automotive, aerospace, and electronics.
Applications of High Pressure Die Casting
High pressure die casting is utilized in several industries due to its efficiency and accuracy:
1. Automotive Industry
In the automotive sector, high pressure die casting is used for components such as engine blocks, transmission cases, and structural parts. The ability to create complex shapes with lightweight materials contributes to fuel efficiency and overall vehicle performance.
2. Aerospace Sector
Aerospace applications demand high performance and lightweight components. High pressure die casting molds are used to manufacture intricate parts that meet stringent safety and durability standards.
3. Electronics
With the rise of consumer electronics, manufacturers rely on high pressure die casting for producing housings and structural components that necessitate cooling efficiency and aesthetic appeal.
The Technology Behind High Pressure Die Casting Mold
The innovation in high pressure die casting mold technology has led to significant advancements in materials and processes. Here are a few key components driving this field:
1. Improved Mold Materials
Modern die casting molds are made from durable materials that withstand high temperatures and pressures, ensuring longevity and quality results. Materials such as H13 tool steel or aluminum alloys are commonly used.
2. Automation in the Casting Process
Automation has revolutionized the die casting process. Automated systems ensure consistent pressure application and precise timing, enhancing the overall efficiency. Robots can undertake tasks from injecting molten metal to handling the finished product.
3. Simulation Technology
Advanced simulation software helps in predicting the flow of molten metal, allowing engineers to optimize mold designs and enhance manufacturability before physical production begins.
Future of High Pressure Die Casting Mold
The future of high pressure die casting mold looks promising due to ongoing research and development:
Sustainability Initiatives
Manufacturers are focusing on sustainability. The use of recycled materials for die casting and energy-efficient processes are becoming common practices.
Increasing Demand in Emerging Markets
As manufacturing technology evolves, the demand for high-quality metal parts is increasing in emerging markets, driving the growth of the high pressure die casting industry globally.
Integration with Industry 4.0
The integration of IoT (Internet of Things) in manufacturing allows real-time monitoring and analysis, optimizing the die casting process and reducing defects significantly.
Conclusion
In conclusion, the high pressure die casting mold represents an essential technique in the metal fabrication industry. Its ability to produce precise, complex, and durable parts efficiently cannot be overstated. With continual advancements in technology and a focus on sustainability, high pressure die casting is poised to remain a critical component in the manufacture of high-quality metal products across various sectors. As industries continue to evolve, so will the capabilities and applications of high pressure die casting molds, making them integral to the future of engineering and production.
For businesses looking to invest in reliable metal fabrication processes, exploring high pressure die casting options can yield significant benefits. Whether it's for automotive components, aerospace structures, or consumer electronics, the high pressure die casting mold is a solution worth considering.